Particleboard VS MDF: 10 Differences You Must Know
Particleboard and MDF are common materials for making home and office furniture. They share similarities in many properties such as constituents, manufacture process and durability. Some of LUMI’s products such as sit-stand desk converters, workstations, monitor risers are available in both types of material. In order to help you choose the most suitable material for your customers, this article will go through the following topics regarding to these two wood products:
· What is Particleboard?
· What is MDF?
· 10 Differences between Particleboard and MDF?
· FAQ
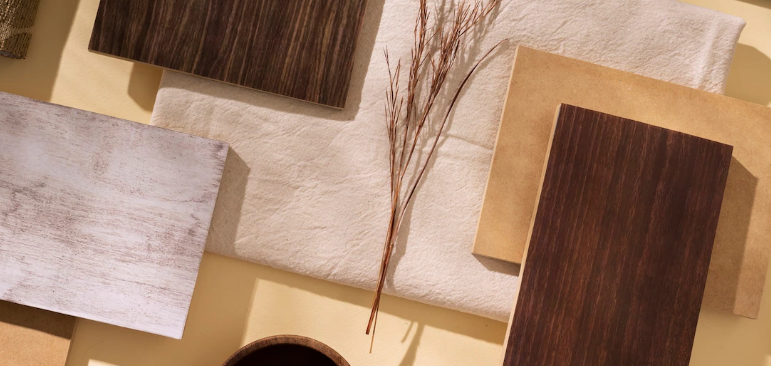
PART 1: What is Particleboard?
Material:
Particleboard (also called chipboard or low-density fiberboard) is made from three main materials: (1) 83% - 88% of coarsely ground recycled wood shavings, flakes, wafers, chips, sawdust, strands, and slivers; (2) 6% - 8% of formaldehyde-based epoxy resins; (3) 5% -7% of water; (4) 1% - 2% non-toxic wax.
Manufacturing process:
(1) Wood fibers are mixed with resin and (2) then pressed under high temperature.
Main Types of particleboards:
(1) Single-layer particleboard (a thin board comprising wood particles of the same size)
(2) Three-layer particleboard (a layer of large wood particles is sandwiched between two layers of smaller particles, making the board more durable and stronger)
(3) Graded density particleboard (a layer of coarse wood chips sandwiched between two layers of softer wood fibers, forming a board that is slightly denser than single-layer but still lighter than three-layer)
(4) Cement particleboard (a mixture of small wooden particles, high-quality cement, and additives)
(5) Laminated particleboard (Laminated particleboard is created by covering a piece of ordinary particleboard with a thin laminate sheet. It boosts the longevity of the particleboard while also enhancing its appearance.)
(6) Melamine particleboard (Melamine particleboard is a plastic-coated material that costs less than laminated panels but offers various options of texture and color. The surface and special chemicals mixed with wood fibers also protect the board from termites and other insects.)
Grading System:
You can tell the quality of particleboards by looking at the grades they received: A, B, C, D, and G1S. This grading system is published by APA The Engineered Wood Association, from which boards will receive a stamp implying the grade. Boards with premium quality fall into the category of Grade A, meaning the defects like burls, knots, and patches are almost unremarkable. Meanwhile, boards with more noticeable appearance flaws are classified gradually down from B to D. G1S, short for good on one side, presents that the board has one smooth and knot free side.
In Europe, particleboards must be specified in accordance with BS EN 312, which contains the requirement for the 7 grades:
● P1: general purpose boards for use in dry conditions
● P2: boards for interior fitments (including furniture) for use in dry conditions
● P3: non load-bearing boards for use in humid conditions
● P4: load-bearing boards for use in dry conditions
● P5: load-bearing boards for use in humid conditions
● P6: heavy duty load-bearing boards for use in dry conditions
● P7: heavy duty load-bearing boards for use in humid conditions
Common particleboard products:
● Particleboards tend to be used on economical products and thus is the best choice for customers who have tight budget. However, it doesn’t mean particleboard products look cheap because with surface process will give it a high-end finish.
● As particleboard is more lightweight, it is an ideal material for portable products. Particleboard can absorb sound. This is the reason why it is used on walls and floors of recording studios, auditoriums, and media rooms.
● Particleboard has a good screw-holding capacity. Thus, it is an ideal material for making the core of door since hinges need to be firmly fixed on the board.
● Particleboards are commonly used as false ceilings because they provide good thermal insulation.
PART 2: What is MDF?
Materials:
Just like particleboard, MDF (also known as medium-density fiberboard) is a reconstituted wood product. And typical constituents of MDF are:
(1) 82% of wood fibers of the same size;
(2) 10% of synthetic resin binder;
(3) 7% of water;
(4) less than 1% paraffin wax solids;
(5) less than 0.05% silicon.
Manufacturing process:
(1) Wood fibers are first processed to fine grains with uniform size before they are dehydrated.
(2) These wood fibers are mixed with resin and
(3) then pressed under high temperature.
Main Types of MDF:
MDF boards are can be classified on the basis of features, such as moisture resistant MDF (desire for wet areas), fire retardant MDF (suitable for kitchen), and ultra-light MDF (mostly used for making furniture). Coated panels are differentiated according to the finishing. For example, veneered MDF is manufactured by compressing a layer of thick hardwood around MDF to create a smooth surface similar to natural wood. Laminated MDF can be used as a whiteboard-like tabletop, for taking notes any time. Meanwhile the surface is easy to clean. It is also a suitable material for children’s desk since it offers a large canvas for doodles.
Grading System:
● MDF can be roughly divided into two grades: interior grade and exterior grade. In Europe, MDF must be specified in accordance with BS EN 622, which contains a more specific grading system:
● MDF: General purpose boards for dry conditions
● MDF.H: General purpose boards for humid conditions
● MDF.LA: Load-bearing boards for dry conditions
● MDF.HLS: Load-bearing boards for humid conditions (These panels are restricted under humid conditions to instantaneous or short periods of loading)
● L-MDF: Light MDF boards for dry conditions
● L.MDF.H: Light MDF boards for humid conditions
● UL1-MDF: Ultra-light MDF boards for dry conditions
● UL2-MDF: Ultra-light MDF boards for dry conditions
● MDF.RWH: MDF for rigid underlays in roofs and walls
Common MDF products:
● Lightweight MDF board is used to make products that require mobility, such as mobile house, trade show booths and modular furniture.
● Featuring soundproofing properties, MDF is an ideal material for preventing sound from traveling through it, so it is widely used for speaker casing, media room and apartment walls.
● As MDF has exceptional durability and weight capacity, it is used to make cabinets, shelves, and other storage units.
PART 3: 10 Differences between Particleboard and MDF
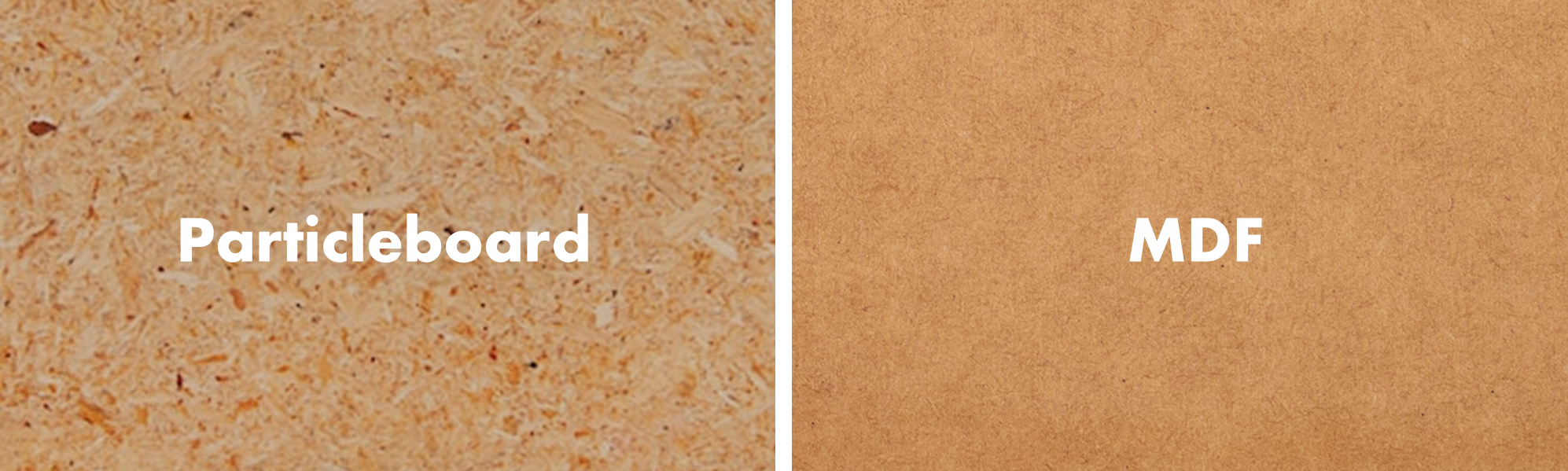
1. Materials: Both particleboard and MDF are engineered from wood fibers that are mixed with synthetic resin adhesives. However, they are mainly different in the size and types of wood fibers: MDF comprises smaller wood particles in the uniformed size.
2. Surface: The surface of MDF is smooth because it is manufactured by pressing small wood particles of the same size, which makes the panel extremely flat and even. On the other hand, particle board has coarse surface and rough edge due to the various size of wood fibers.
3. Density: The average density of particleboard (600-680 kg/m3) is slightly lower than MDF (700-800 kg/m3). Therefore, particleboard is lighter when compared to MDF in the same size.
4. Load bearing capacity: MDF has larger weight capacity than particleboard.
5. Strength and durability: MDF is fairly stronger and more durable than particleboard owning to the high density of wood fibers.
6. Outdoor use: Although both MDF and particleboard are not 100% water resistant, with proper surface finishing they can be not susceptible to water damage. It is noticeable that even coated particleboard can be destroyed due to moisture; thus, it is not recommended for outdoor use. Comparatively, MDF with coating is more resistant to moisture, rotting as well as insects and can be used for making doors exposed to the nature.
7. Cost: Particleboard is more cost effective compared to MDF with the same size and thickness.
8. Life Span: Furniture made of MDF are expected to last for decades. Laminated MDF is estimated to have 15-20-year life span with proper care. For particleboard, it has less life span but still can last for 10-15 years.
9. Easy to cut: MDF is comparatively difficult to cut and mill because it is more dense under high pressure.
10. Capacity to hold a screw: Since MDF is made up of fine grains, it cannot hold a screw as steadily as particleboard.
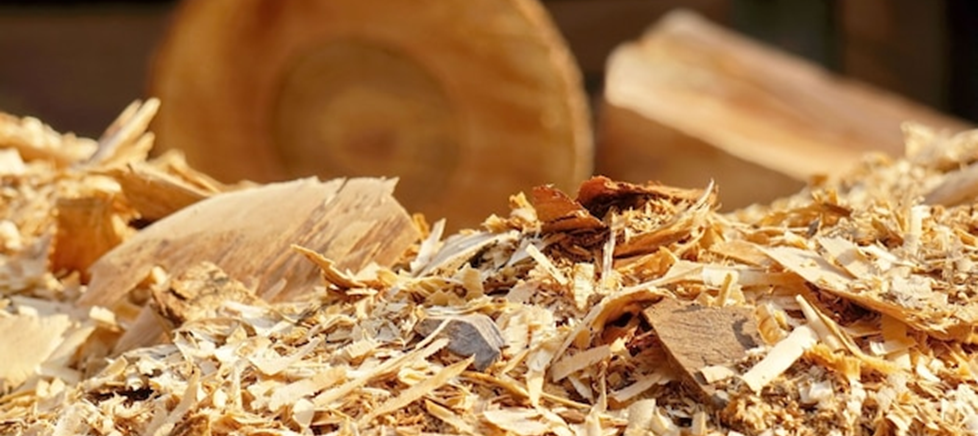
PART 4: FAQ
Q: Are MDF and particleboard eco-friendly?
A: Yes. As waste wood products, they are made by recycled wood waste.
Q: Are MDF and particleboard stronger than solid wood?
A: Compared with natural wood, these two engineered products gain advantages in terms of fire redundant and dimension stability – they won’t expand or contract when temperature or humidity changes.
Q: Is particleboard/MDF free from biological attack?
A: Both types of pressed wood products are not likely to be attacked by wood-boring insects. However, under humid conditions, they might be vulnerable for fungal attack.
Q: Is particleboard/MDF toxic?
A: In most cases, they are not toxic. But still, it is important to make sure the products you order are compliant with specific quality standards. Check out whether your supplier provides USA CARB and EU E1 test report.
In a nut shell, both MDF and particleboard are waste wood product that made of pressed wood particles. Generally speaking, MDF is considered as a superior material compared with particleboard, while particleboard is a super affordable option for budget-saving customers and is preferred as a cheaper alternative to MDF.